Кувалдой по капоту («российская газета»)
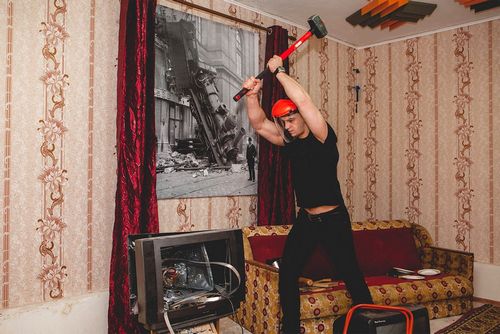
Курс на понижение выбросов углекислого газа в воздух, взятый в большинстве стран мира, коснулся не только фирм энергетического сектора. Согласно расчетам специалистов, более 60 процентов от общего объема эмиссии в "активе" транспортных средств, трудящихся на классическом моторном горючем (бензин, солярка, газ).
Снизить его потребление, а вместе с тем и вредные выбросы, возможно, облегчив конструкцию ТС. Этим благополучно и занимаются предприятия мирового автопрома. Многие автовладельцы со стажем точно уже увидели, что толщина стали в кузовах автомобилей делается меньше.
Но таковой подход чреват понижением пассажиров безопасности и уровня водителя. Как же автомобилю "похудеть" без негативных последствий?
Весьма : часть "железа" полимерными материалами — более воздушными по массе и не меньше прочными.
Полиуретаны, поливинилхлориды, полипропилены, полиэтилены в чистом виде и в виде композиций, полимерные композитные материалы — стеклопластики, углепластики, органопластики и базальтопластики — все эти продукты органической химии сейчас находят широкое использование в автопроме, а также в несущих и ходовых частях современных "ласточек". Эта тенденция характерна как для мировых, так и для русских брендов.
Так, один из фаворитов европейского автопрома компания Scania, открывшая в 2012 году завод по сборке грузовиков в Шушарах, применяет пластиковые подробности для интерьера кабин и дизайнерских элементов экстерьера. "Из литого PPO/PS (оксид полисульфата + полистирол) изготовлены крылья, бамперы, защита двигателя, корпуса зеркал. Для навесных элементов кабины, каковые не воздействуют на безопасность, употребляются стеклопластики.
Из них изготовлены уголки капота, боковая защита и спойлеры.
На автобусах изготавливают заднюю маску и переднюю из стеклопластика, на модели Omni Express — панели боковины, — сказал "РГ" эксперт-консультант по техническим вопросам "Скания-Русь" Максим Левинсон. — Пластик, в отличие от металла, не подвержен коррозии и достаточно долговечен. Существуют кое-какие сложности с его окраской, но они разрешаются".
"Композиты намного легче, чем металлы, а следовательно, дают экономию за счет понижения затрат на установку, и облегчают работу и снижают расход горючего. К тому же жесткость композитов сравнима, а время от времени и лучше, чем у алюминия и стали", — дополняет сотрудника начальник отдела маркетинга продукции "Ивеко Руссия" Николай Лебедев.
Композиты, утверждает специалист, являются хорошими термоизоляторами и демонстрируют хорошую стабильность формы. Они не становятся хрупкими на морозе, а при ДТП легко возвращают собственную форму.
"Кроме этого хотелось бы отметить их устойчивость к широкому спектру веществ и дорожных реагентов, — выделил Лебедев. Новейшие способы производства панелей разрешают окрашивать подробности сразу после углубления из формы и без подготовки к окраске.
Композиты разрешают разрабатывать универсальные легкие конструкции, благодаря чему вероятно снизить массу автомобиля и оптимизировать процесс производства".
Один из таких проектов — мини-вэн, созданный компаниями Advanced Composites Group ЛТД. (ACG) и Emerald Automotive. Главным преимуществом от применения композитов разработчики именуют понижение выбросов и потребления топлива — до 80 процентов если сравнивать с аналогами.
Не спят и отечественные производители машин. Как сообщили в Группе ГАЗ, полимерные подробности активно используются для того чтобы интерьера кабины, бачков и сцепления и систем термостойких патрубков двигателя, клапанной крышки и вентилятора двигателя, фонарей и корпусов зеркал, солнцезащитных козырьков, трубопроводов тормозной сцепления и системы, брызговиков и крыльев, корпуса и рассеивателей устройств.
В оперении автомобиля нового поколения "Урал NEXT", производство которого началось в 2015 году, применены современные литьевые полимеры, имеющие высокие механические особенности и снабжающие технологичность производства — полиамид (PA) и полидициклопентадиен (PDCPD). Пластики по большей части русского производства.
На организованном автозаводом "Урал" прошлым летом тест-драйве в условиях, максимально приближенных к настоящим, его участники кроме другого испытывали полимерный капот грузовика на прочность. Ударяли по нему тяжелыми молотками по паре десятков раз, наряду с этим ни мельчайшего следа деформации на капоте не появилось.
Но в случае если производители грузовых авто разглядывают всецело композитную кабину лишь как возможность, то легковой "пластмассовый" автомобиль уже сконструирован!
Это сити-кар Mirrow Provocator русского компании Mirrowcars. Причем, как согласился "РГ" основатель компании Александр Малышев, работа над этим авто изначально не имела цели применять в его кузове полимеры.
Такое ответ пришло позднее, как желание снизить вес кузова.
И кардинальное отличие от современных полимерных элементов кузова машин (крыльев и т.п.) содержится в том, что в "Провокаторе" полимеры смогут употребляться не только во внешних элементах, но и в силовом каркасе, что фактически нереально в простых кузовах.
"Эта возможность показалась за счет того, что кузов воображает силовую ферму с солидным числом маленьких силовых элементов. И на протяжении работы стало ясно, что не все эти элементы должны быть из металла.
В случае если в определенных местах вместо силовой балки из металла применять комбинированный сэндвич из полимеров и металла, а в некоторых — лишь из полимеров, мы не проиграем в жесткости кузова, но победим в понижении веса и в более действенном распределении энергии удара при аварии, — сказал Малышев. — В итоге, по моим расчетам, часть полимеров в кузове "Провокатора" сейчас около 50 процентов. Наряду с этим чем выше подробность от почвы, тем часть полимеров выше.
Пологаю, что через 10-15 лет по окончании начала серийного производства таких автомобилей часть полимеров в их кузовах вырастет до 75-80 процентов. А при доле полимеров в кузове более 75 процентов автомобиль уже можно считать пластиковым, а не железным".
Через 5-7 лет, считает Александр Малышев, автопром ожидают громадные трансформации. Химические фирмы начнут поставлять фабрикам готовые полимерные кузова, а конкретный производитель будет ставить в том направлении личные агрегаты, наклеивать логотип и реализовывать в собственных салонах.
"Пологаю, что через 15-20 лет полимерные легковые авто начнут господствовать на рынке новых машин. Обстоятельствами для бурного роста этого сегмента смогут являться меньшая себестоимость производства кузовов и снижение цен на нефтяном рынке, что должно стимулировать компании нефтехимии на развитие новых рынков сбыта.
И автопром может стать тут одним из главных потребителей", — выделил специалист.
Сейчас нельзя не упомянуть и о роли полимерных материалов в интерьере автомобиля, поскольку водители все больше значения придают личным и персонализированным элементам интерьера.
Под этим подразумеваются приятное освещение, ровные бесшовные соединения, прозрачные, цветные либо декорированные поверхности. Исходя из этого производители полимерного сырья в сотрудничестве с производителями машин трудятся над комплексными концепциями материалов для отделки автоинтерьера.
"Сейчас в моде расширенная функциональность и информационно-развлекательные возможности — все это в совершенном выполнении и с дорогостоящим внешним видом", — отмечает Александр Широков, эксперт по автопрома в бизнес-подразделении по производству поликарбонатов русского представительства Covestro, компании, которая создала комплексную концепцию рентабельного дизайна на базе поликарбоната, что всецело удовлетворяет этим требованиям. Один из примеров — инновационные дисплеи с однородной трехмерной поверхностью, но одновременно с этим с высокой яркостью и чётким изображением.
Это произошло благодаря разработке обратной проекции, в то время, когда источник света за пленкой превращает ее в подсвеченный экран. Специально для этого была создана поликарбонатная пленка Makrofol™ RP (RP — сокращение от Ruckprojektion — "обратная проекция". — Ред.). "Эта разработка знаменует собой совсем новый тип информирования водителя: на дисплее будет отражаться лишь то, что он сам выберет", — растолковывает Александр Широков.
В отключённом состоянии дисплей выглядит как элегантная тёмная матовая поверхность. Водителя не отвлекают другие эффекты и внутренние детали.
Возможно привести множество примеров вторых идей, среди которых — применение подсветки в декоративных премиум-элементах, к примеру с натуральным шпоном, либо узкое легкое сиденье с разнообразными вариантами декора на базе сравнительно не так давно созданной панели из поликарбонатной композитной смеси.
"Для автопрома выгодно как многообразие вариантов дизайна, так и экономически действенное производство подробностей", — резюмирует специалист.
Ну и, само собой разумеется, будем помнить о таком ответственном применении в автопроме пенополиуретана (в обиходе — поролон), как наполнителя автомобильных сидений. С содроганием отыщем в памяти продавленные "пятой точкой" пассажиров и водителя за много лет эксплуатации кресла в отечественных машинах выпуска середины прошлого века.
И порадуемся за современные модели автосидений, сохраняющих изначальную форму десятилетиями благодаря прогрессу в химической отрасли и снабжающих водителю комфорт кроме того в самой дальней дороге.
«Русский газета»